Szkło prasowane wg Drosta
Szkło prasowane
HSG „Ząbkowice” S. A.
(wzornictwo i technologia)
Autor: Jan Sylwester Drost
Technika prasowania szkła rozpowszechniona szeroko na skalę produkcyjną z początkiem XIX wieku jako jedna z pierwszych przyczyniła się do powstania taniej i masowej produkcji wyrobów ze szkła poprzez mechaniczne wytwarzanie. Pierwsze wyroby ze szkła prasowanego nie zawsze były celowo kształtowanymi przedmiotami i znajdowały się też długi czas poza kręgiem zainteresowań.
Stosowano przeważnie formy i dekory pseudostylowe z przypadkowo zestawionymi motywami zdobniczymi oraz bardzo mierne kopie szlifów kryształowych.
Na rynku znalazły się tanie, pozbawione indywidualnego wzoru a często i wartości estetycznych artykuły szkła prasowanego. Jakość przeszła w ilość i nie może dziwić fakt, że szkła tego typu nazywano z lekceważeniem „szkłem dla ubogich”. Niektóre tylko szkła prasowane, a zwłaszcza secesyjne czy szkło z lat 20. zwróciły na siebie uwagę swoją oryginalnością.
Dopiero z czasem w niektórych większych ośrodkach szklarskich w Europie podjęto skromne próby nowego podejścia do rozwiązań projektowych w zakresie szkła prasowanego. Niełatwe to zadanie, ponieważ artystyczne punkty widzenia bardzo mocno ograniczają procesy technologiczne.
Projektantów zawsze nurtował problem znalezienia właściwych dla tej techniki wytwarzania szkła nowych form plastycznych, które obok walorów użytkowych, mimo wielkiej ilości egzemplarzy powstałych przez ich dokładne powielanie, miałyby również wysokie walory estetyczne i artystyczne towarzyszące formom współczesnego wzornictwa przemysłowego. Projektanci, znając też zapotrzebowanie rynku i społeczną ocenę ich pracy kształtują swoje dzieła we współzależności ogólnego rozwoju dyscypliny fachowej, w której zakresie tworzą tak, aby zrealizowane wybory finalne wyróżniały się nie tylko dobrą formą plastyczną, funkcjonalnością i nowatorskimi cechami produkcyjno-technologicznymi, ale stanowiły także wartość społeczną i kulturową.
Dlatego naszym podstawowym założeniem w zakresie projektowania szkła ręcznie prasowanego seryjnie było ugruntowanie własnego kierunku poszukiwań twórczych poprzez wykreowanie i stosowanie nowych form i elementów zdobniczych zapewniających dobre efekty optyczne i plastyczne charakterystyczne dla tej technologii produkcji i niemożliwe do zrealizowania żadną inną techniką formowania szkła.
W ramach tego programu przez umiejętne połączenie wiedzy o technologiczno-produkcyjnych możliwościach formowania szkła prasowanego z artystycznymi przemyśleniami, opracowano wiele kolejnych nowych, estetycznych i funkcjonalnych wyrobów stanowiących pokaźną cząstkę polskiego wzornictwa szkła, które wielokrotnie było wyróżniane w konkursach i pokazach. Znalazły też wysokie uznanie na wielu specjalistycznych imprezach handlowych w kraju i za granicą.Było to możliwe dzięki stałej współpracy projektantów ze specjalistami w zakresie technologii szkła, konstrukcji metalowych form szklarskich i z zespołami hutniczymi – mistrzami rękodzieła szklarskiego.
Formowanie szkła metodą ręcznego prasowania umożliwia dzięki dalszej obróbce termicznej i zastosowaniu prostych narzędzi hutniczych na kontynuowanie ręcznego kształtowania wyrobów nadając im w ten sposób indywidualny wyraz i wdzięk.
Wykorzystanie nowych metod obróbki metali w pracach przygotowania form szklarskich przez zastosowanie form z gotową zdobiną pozwoliło projektantom na wiele oryginalnych rozwiązań zdobniczych. Przykładem może być dekoracyjny zestaw szkła prasowanego „Diatret” nagrodzony złotym medalem na I Międzynarodowym Triennale Szkła i Porcelany Jablonec – 1973 prasowany ręcznie w formach wykonanych metodą drążenia elektroiskrowego.
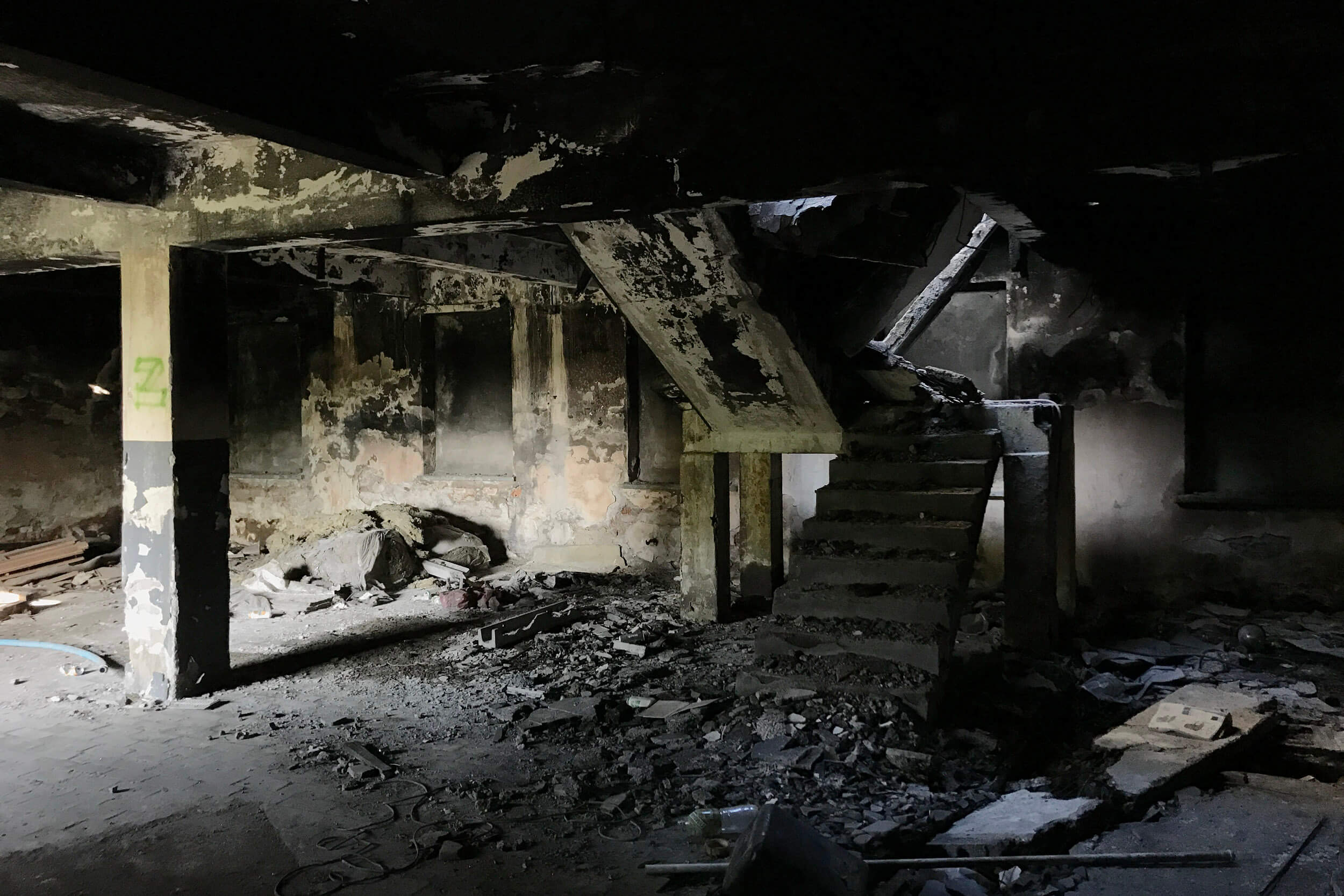
Inne ciekawe rozwiązania wzornicze uzyskano dzięki zastosowaniu ukształtowanym odpowiednio przez obróbkę maszynową powierzchni zewnętrznej tłocznika i wewnętrznej formy żeliwnej. Efektem tego były regularne względnie asymetryczne soczewki dwustronnie wklęsłe albo inne nakładające czy też przenikające się o ciekawych, wyszukanych układach graficznych i doskonałych efektach optycznych dekory.
Metoda odlewnicza pozwalająca na wykonanie żeliwnych form szklarskich bezpośrednio z przygotowanych modeli przestrzennych stworzyła przed projektantami nieograniczone możliwości indywidualnego wypowiedzenia się. Wykorzystanie nowych tworzyw i mas plastycznych pozwoliło z jednej strony na precyzyjne przygotowanie modeli prototypów z dowolnymi strukturami powierzchniowymi przypominającymi różne faktury np. ziarnistą piasku, kory i słoi drzew, skorup muszli itp. a z drugiej strony na formowanie w szkle płaskorzeźb jak i kompozycji przestrzennych – figurek i rzeźb.
Te możliwości formowania przestrzennego i kształtowania wypukłych struktur na zewnętrznych ścianach prasowanych naczyń szklanych pozwoliły projektantom na szereg oryginalnych rozwiązań plastycznych o trwałych wartościach rzeźbiarskich.
Wypracowanie nowych koncepcji wzorniczych dla szkła prasowanego seryjnie nie kończy się bynajmniej na przygotowaniu nowych form i dekorów, ale polega również na znalezieniu nowych niekonwencjonalnych metod pracy i stałego doskonalenia technik i technologii. Zadania te nie są proste ani łatwe jeżeli przy tym muszą być uwzględnione wymogi techniczno-produkcyjne, estetyczne, jak również i ekonomiczne.
Wieloseryjna produkcja zobowiązuje też projektantów szczególnie do dużej dyscypliny, ponieważ każdy błąd może się powielić w tysiącach egzemplarzy.
Projektanci zainspirowani modelowaniem dekoracyjnych medalionów ze szkła opracowali założenie konstrukcyjne do nowej generacji form szklarskich tzw. form otwartych do ręcznego prasowania szkła. Zastosowanie tych form i opanowanie prasowania wyrobów nową metodą przez zespoły hutnicze pozwoliło na wykreowanie z początkiem lat 60. pierwszych wielofunkcyjnych wyrobów o bardzo płynnej i łagodnej linii górnego obrzeża. Przykładem jest zestaw szkła prasowanego ręcznie „Asteroid”, którego część – talerze nagrodzono złotym medalem na II Międzynarodowym Triennale Szkła i Porcelany – Jablonec ‘76 w Czechosłowacji.
Metoda ta opatentowana i stosowana od lat szeroko na skalę produkcyjną w Hucie Szkła Gospodarczego „Ząbkowice” a później w innych hutach szkła pozwoliła na rozwinięcie nowego kierunku projektowania wyrobów i zapewniła też znaczne efekty ekonomiczne poprzez zmniejszenie składu osobowego zespołów hutniczych, całkowite wyeliminowanie uciążliwych i kosztownych metod obróbki termicznej oraz mechanicznej – szlifowanie i polerowanie. Ciekawe wyniki przyniosły dalsze eksperymenty podczas formowania wyrobów prasowanych ręcznie w tzw. formach otwartych z dwubarwnymi masami szkła. Wprowadzono tu dwie metody, które sprawdziły się i przyniosły dobre wyniki w produkcji seryjnej.
Przez podanie nabierakiem kulowym dwóch uzupełniających się kolorystycznie mas szkła uzyskano dekoracyjne wyroby prasowane cieniowane gradalnie zaś w drugim przypadku przez ułożenie dwóch mas barwnych, jednej w układzie podłużnym a drugiej centralnie w kształcie kropli, otrzymano obok efektu malarskiego również oryginalną formę plastyczną. Przykładem jest zestaw talerzy „Smuga” nagrodzony złotym medalem na II Międzynarodowym Triennale Szkła i Porcelany – Jablonec ‘76 w Czechosłowacji.
Szkło prasowane otrzymuje nowe bogate oblicze twórcze. Całkowita automatyzacja procesów technologiczno–produkcyjnych w zakresie wielkoseryjnego formowania wyrobów codziennego użytku ze szkła sprawiła, że w ciągu ostatniego 30-lecia tradycyjne szkło prasowane wytwarzane nadal ręcznie, częściowo zdobione przez matowanie trawieniem lub strumieniem piasku oraz ręcznym malowaniem przestało być szkłem o niskim standardzie. Dzięki umiejętnemu połączeniu tradycji rękodzieła artystycznego, nowatorskich technologii, technik formowania, zdobienia i wyróżniającego się wzornictwa Huta Szkła Gospodarczego „Ząbkowice” S.A. zawdzięcza swój prestiż na rynku krajowym oraz rynkach zagranicznych krajów europejskich i zamorskich.